xRM for Manufacturing
Production. Shipping. Quality Control.
Small and medium-sized manufacturing companies, whether they produce widgets or wedges, face similar production challenges. Communication between departments breaks down. Antiquated manual paperwork slows the process. Record keeping and documentation for industry or government certifications is cumbersome. If your manufacturing company is focused on filling orders and growth rather than operational efficiency, you’re not alone. But one does not have to be sacrificed for the other. A P2 xRM computer system that automates repetitive tasks, speeds communication between departments, and keeps track of all of the parts and pieces that go into producing a saleable product is possible.
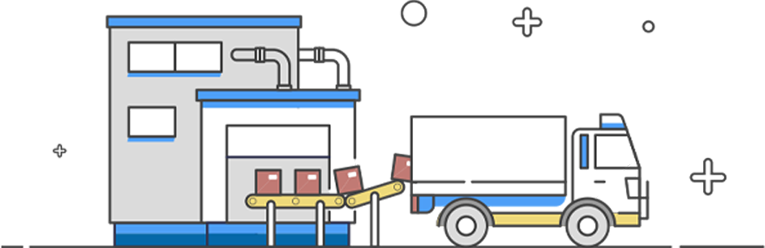
Common Manufacturing Challenges
- Slow production or order processing
- Inaccuracy in fulfilling orders
- Hit-or-miss customer service
- Antiquated manual handwritten workflows
- Inter-departmental communications breakdowns
- Inefficiencies while tracking documentation for government or industry certifications
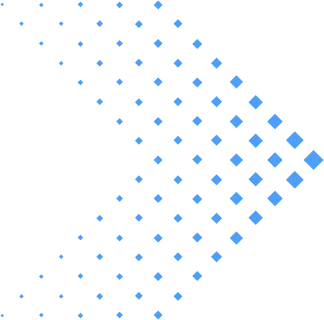
P2 Automation
Solutions for
Manufacturing
Automated Production Requests
Rather than relying on paper forms or tickets, a P2 Automation xRM system can automate production requests and digitally track orders as they come in, check inventory for missing pieces, and notify the shop floor staff that a product needs to be built.
Track KPIs
If your factory needs to track key performance indicators or certifications like ISO 9001, or others, having that info available on a digital dashboard, rather than hunting through papers and spreadsheets, saves time and improves efficiency.
Real-Time Dashboards
Once a product is built, production staff uses a barcode scanner to mark it as complete, or that a particular stage of production is complete, moving it down the assembly line where Quality Control will be notified that it is ready for inspection. No waiting. No guessing. Each step in the assembly process is checked off and recorded.
Bar Coded Inventory Labels for Inventory Control
Know exactly how many of each component you have on-hand. Tracking inventory on paper is unwieldy and inefficient. Using barcode technology tied into your company’s xRM tells you at a glance what you have, and what you don’t have in stock.
Increase On-Time Delivery Metrics
Deadlines are critical in manufacturing and production. Your customer wants the product when they want it, not when you can get it to them. To help improve on-time delivery, alerts and flags within your xRM system serve as guides and motivators to help your team stay on-task and on-time.
Integration with Related Systems
Using the Microsoft Power Platform as the base software, your xRM system can be integrated with your existing software to populate your factory’s customer records, customer orders and history.
Quick User Adoption
Simple and easy-to-read dashboards make the transition to your new system a breeze for your employees. We can mirror existing color-coding systems that are already in place on your production floor to keep visual cues consistent.
What Our Manufacturing Customers Say About Their xRM Systems
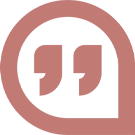
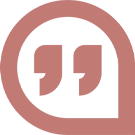